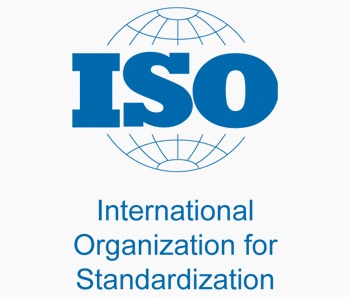
前回は「目標設定」の重要性を述べました
この章では「QC工程図」について掘り下げます。
工業界のもの作り民主化が進んだ功労は「マニュアル(標準化)」が
進んだ事と言っても過言ではありません。
この「マニュアル」にも落とし穴がございます。
例えば貴方が現場担当であった場合
上司から「これからは属人化を無くし、誰でも作業を行える様にマニュアル化を進めなさい」
これだけの指示を受けた場合、どのように感じますか?
どこから手を付けるか?全部作るには工数がかかるな
面倒だな…、何をマニュアルにするのかな
このようなモチベーションで
「とりあえず指示を受けたから出来る所から作ろう」
このような状況を多く見ています。
今この内容を見ている貴方「身に覚え無いですか(笑)」
そうなんですよ
一口に「マニュアル化」とは言え難しく
何をするか?何を伝えるか。
誰に伝えるか?目的は何?
これらをないがしろに進める事が多く
これが原因で使えない、使わないマニュアルがムダに大量生産される訳です。
もっと言うと残業までして形骸化資料を作らされている訳です。
はい、回答です。「QC工程図」をサクッと書きましょう。
QC工程図とは
製品の投入(工程IN)から出荷(工程OUT)までの
フローチャートを書きましょうです。
QC工程図には一定のルールがあります
ここは弊社登録の講師にお任せ下さい(笑
製造の流れ、検査箇所、検査内容、使用設備…これらのフローチャートです。
大量生産ではなく単品生産であれば主要製品のモデルでも大丈夫です。
この作業のフローが分かると
・どこの作業が重要か
・検査の妥当性、検査の重要性
・作業のボトルネックは
・特に品質、作業性の影響する箇所
この辺が俯瞰的に理解出来ます。作業の羅針盤ですね
これが出来れば次の指示は明確です。
重要な部分をピックアップして
先ずはそこだけ(これ重要)
作業手順書、検査手順書、検査判定基準この辺を作成します。
その中でも特に注意を促す部分を太字、赤文字表記して
作業する方に教育するのです。
教育した際に「誰にいつ教育したよ」的な台帳が出来れば
教育台帳のエビデンスも完了です。
もっと言うと、この指示を出す事で本質的な指示になり
ムダな資料の作成に時間を取られる事が激減します。
そもそもこれが出来ていないので根本的な「働き方改革」が出来ない
曖昧な仕事負担の増加です。
多くのISO取得会社では出来ているとは思いながらも
意外に出来ていない現状も見ています。
是非心当たりがある会社や経営者さま
先ずはここから見直しませんか?
「QC工程図」にもテクニックが必要です
この辺は専門家がアドバイスさせて頂きます
言い方は乱暴です、ムダに費用や工数をかけているのであれば
この上流に費用をかけた方が大きな資産になります。
気概のある経営者の方
「貴方の会社の困ったに寄り添います」
現場からは以上です。