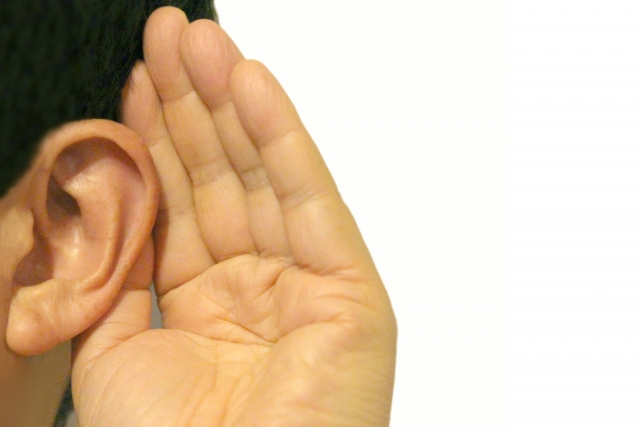
「よそ者、若者、ばか者」と言う言葉があります。
同じ場所で同じメンバーで真面目な方々で知恵を出し合っても
堂々巡りになる事があるので、
煮詰まった場合は
「よそ者の客観的に世代を超えて意見を問い、違った目線で」
と言うニュアンスかと思います。
これは様々な場面で有効です。
弊社は企業OBの方に登録頂き、主に製造業の生産性向上訓練をさせて頂いております。
その中で、企業様の要望で「弊社と同様の業種経験がある講師」
と言うのが良くあります。
もちろん依頼者の気持ちは理解します。
自社の課題解決に同業他社の事例や経験を活かして研修して欲しい
これはあながち間違っていませんが
経験的には違うケースが多々あります。
折角の研修の機会ですので、異業種経験の講師に依頼することの方が
問題解決の糸口に近づく事が多いです。
製造業と言う括りで見ると「人、設備、環境(材料含む)」に尽きます。
各々の専門技術は違えど、違う観点は重要です。
自動車部品工場と食品加工業
部品塗装業種と半導体製造業
バッチ加工製造会社とライン加工製造会社
事例になりますが、この様な異業種コラボはかなり有効です。
自動車関連業種は比較的、トヨタ品質改善手法を学んだりしています
しかし同じ製造業でも食品加工業は製品が違うだけでトヨタ手法は全然関係ない
と思い込んでいる節があり、5Sとかカイゼンを未経験が多い(傾向です)
製品は違えどモノづくりは一緒です、是非活用すべきです。
塗装系会社の課題は塗装時のダスト付着不良です
ダスト不良と一口で言っても大量の論文やクリーン化技術が必要な分野です。
ダスト改善は半導体製造業経験者に聞きましょう。
半導体工場のクリーン化に比べれば、塗装上のダストレベルは簡単です。
是非活用頂きたいです。
バッチ加工とライン加工を捉えた場合、製造法も工場構成も違いますが
目の前の作業を切り出した場合の「モノづくり」は一緒です。
そのように捉えると一個流しもライン流しも同じ思想で語れます。
これは今までの経験的な事例ですが
混沌として形骸化した改善活動が活性化しない場合は
是非ともこの「よそ者、若者、ばか者」を意識して進めてみて下さい。